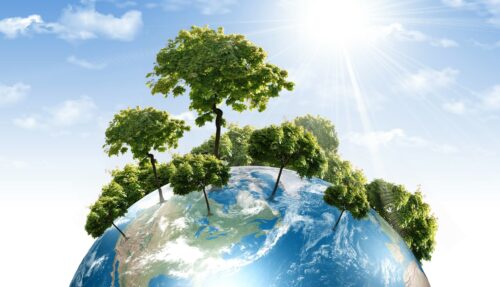
Applying Nuclear Expertise to Solve the Auto Industry’s Challenges
This article was originally printed in the Winter/Spring 2015 edition of Lead, Reach and Connect, which is published twice per year for the Automotive Parts Manufacturers’ Association (APMA). It has been reprinted with permission from the APMA and Matrix Group Publishing Inc. and cannot be reproduced without prior written consent. To view the full edition of the magazine, please go to https://apma.ca/news/publish/finallowresapmawinterspring15websitepdf#content-head.
By Clemente Angiolillo and Daniel Banks

The neutron beamlines at the National Research Universal (NRU) reactor protrude out from the shielding wall around the reactor to allow materials to be analyzed non-destructively in the beams.
Situated two hours northwest of the nation’s capital on the scenic shores of the Ottawa River, Canadian Nuclear Laboratories (CNL), Canada’s national nuclear science and technology organization, has been a key player in the global nuclear sector from its inception over 60 years ago. Through the work done at Chalk River Laboratories, CNL gave the world a uniquely Canadian reactor design known as CANDU, and put forth pioneering innovations in the area of nuclear medicine and environmental remediation technologies, just to name a few areas of expertise.
However, as several auto parts suppliers will attest, the solutions offered by nuclear technologies have application in other industries as well. Today, as the auto industry grapples with many technical challenges to meet stringent fuel efficiency targets— achieved partly by obtaining favourable strength-to-weight ratios for motor vehicles— as well as enhancing quality assurance of parts and components, researchers at CNL are bringing their unique facilities and expertise to the auto industry’s doorsteps, and with remarkable results.

A visiting researcher prepares an advanced in-situ examination of an alloy’s properties under various conditions of applied load on a neutron beamline.
“On the heels of CNL’s participation at the Automotive Parts Manufacturers’ Association (APMA) Annual Conference & Exhibition held in Windsor, ON in early June, we were pleased to announce that we had secured a new customer named AGS Automotive Systems Inc. to perform metallographic and surface analysis of various chrome plated parts,” says Elliott Gillespie, CNL director of marketing and international business.
The recently appointed marketing director says the technical challenge of this commercial contract is to perform indepth studies on the components to locate potential particulate or contaminants residing between very thin material plating layers, thus ensuring optimization of longterm corrosion resistance once the parts are placed in extreme weather conditions. AGS Automotive is a Tier 1 automotive parts supplier (and APMA member) specializing in bumper impact assemblies with capabilities in metal stamping, chrome-plating, Class A painting and welding. The company operates 10 facilities in North America and has approximately one-third of the chromeplated bumper business—producing mainly front and rear impact system assemblies and modules, as well as some general stampings, running boards and exterior painted trim parts such as grills—as sister company Tiercon Corp. Customers include GM, Toyota, Chrysler, Volkswagen and other major original equipment makers.
Years of automotive research

A visiting researcher makes small adjustments to the positioning of a new alloy sample on a neutron beamline to map its properties in three dimensions.
Lest one get the impression that CNL’s work in the automotive parts sector is a recent business activity, think again. Years of research on technologies to make lightweight car engines reliably have been afoot at Chalk River and may soon pay off with big dividends to parts suppliers. In addition, the value of CNL’s contributions to these technologies are being recognized by peer organizations and partners such as the Canadian Academy of Engineering (CAE), who recently bestowed a CNL researcher with a prestigious honour.
Dr. Dimitry Sediako, a Senior Research Officer, was inducted as a Fellow of the CAE in June 2014 in recognition of his contributions to improving manufacturing technologies in engine block casting and heat treatment, among other achievements. According to CNL customer Nemak Canada, these technologies, when implemented, will speed production times and reduce energy usage, thereby saving millions in manufacturing costs.
Some of these achievements and applications strike automotive manufacturers as novel and have potential customers wondering how exactly nuclear technologies can deliver value to the auto parts sector. Part of the formula for success is having diverse supporting facilities and the right expertise, but the other important piece is direct access to industry partners. And then there is the power of neutrons.
The power of neutrons
CNL hosts the only major neutron beam laboratory in Canada at its multipurpose National Research Universal reactor. Neutron beams, like no other tool, can be used to non-destructively probe deep inside engine blocks and determine the amount of stress in the material at any given point, which is a key factor in the reliability of the engine. Having honed this capability for decades, CNL’s researchers are world leaders in using neutron beams to determine properties of metallic materials, and have examined parts for jet engines, car engines, ship hulls, pipelines, bridges, and rail tracks, in addition to parts for nuclear reactors.

Researcher Dr. Dimitry Sediako sets up an engine block for non-destructive examination of residual stress on a neutron beamline at the National Research Universal (NRU) reactor at Canadian Nuclear Laboratories (CNL).
Although not yet standardized in the automotive industry, leading companies are now beginning to make use of this hightech tool. Dr. Sediako has built partnerships with researchers from Nemak Canada, major automotive manufacturers such as General Motors (GM) and Ford Motor Company, four universities (Ryerson University, University of British Columbia, University of Waterloo, McGill University), and Canmet Materials Laboratory, each of which contributed their own tools and expertise in metallurgy, mechanical testing and computer modelling.
In one line of research, Nemak’s objective was to find the best way to build robust V-6 aluminum engine blocks. These engines have extremely low tolerance for distortion in the shape of the cylinder holes in the block. Stress relief methods are used after casting the block to increase stability, and yet each manufacturing step comes with its own costs and impacts on the materials properties. To improve over current manufacturing practices, the team needed to understand more clearly the factors contributing to stability.
Nemak and its research partners from Ryerson University accessed Chalk River’s neutron beams for several studies with Dr. Sediako’s assistance to acquire and interpret the neutron diffraction data. These studies included elucidating the stress distribution and microstructure in new aluminum alloys and in engine blocks, before and after stress relief methods such as heat treatment. Additionally, they included pioneering observations of microstructural evolution during solidification of the alloys.
The results were vital contributions to the success of the research, helping Nemak to determine that simplifying the heat treatment process is feasible without compromising reliability. Nemak is now moving forward to validate the new process by performing final tests before the engine can be used in vehicles sold to customers, such as putting a prototype engine block in a test vehicle.
Neutrons help GM
During a recent webinar organized in conjunction with APMA, CNL worked with Nemak and GM to showcase the application of nuclear technology to develop better engine components, and elaborate on the range of nuclear capabilities available to automotive companies through CNL.
GM uses neutron beams to accelerate the development of engine heads and blocks. These projects span three primary research areas:
• Evaluating effectiveness of heat treatment and quenching methods.
• Directly observing phase precipitation during solidification.
• Creep testing to make better predictions of reliability over the long-term.
In the first area of evaluating effectiveness of heat treatment and quenching methods, neutron experiments clearly falsified a hypothesis for GM that air quenching of cylinder heads would be a benefit over water quenching because of an overall reduction in residual stresses. The results showed significant stresses remained with air quenching deep inside the cylinder heads, at a depth of about one centimetre.
On the second research area of directly observing phase precipitation during solidification, GM uses modelling software to try to predict the properties of the components or alloys after they solidify, but sometimes the models fail to predict the actual results. Neutrons can uniquely identify phases that precipitate during solidification. In other words, they allow GM to “watch” the solidification process experimentally to better understand what is causing the discrepancies.
The third research area is concerned with “creep testing,” which in essence means determining how the shape of the part may change over time and eventually fail or cause problems. The neutron beam experiments allow GM to look at how the arrangement of the atoms is changing in the material to better understand how these changes take place.
Neutrons help Ford
CNL has an ongoing research project with Ford to examine new ways of joining dissimilar materials together to be used in light-weight vehicles. For example, self-piercing riveting (SPR) is a leading alternative to traditional welding methods, and has been widely used by Audi, Mercedes, BMW, and Jaguar, as well as Ford on their aluminum cars and sports utility vehicles. SPR joints have excellent mechanical properties and high fatigue resistance. But the 3D residual stress field in a mixed metal SPR joint had not been experimentally studied before, making prediction of fatigue life of such SPR joints difficult. Ford turned to CNL’s neutron beam capability because other ways of determining stresses were too difficult, considering the complex geometry and number of different materials involved. It plans to use the results from the neutron analysis to validate its existing residual stress prediction method, and document these findings to inform broader manufacturing processes.
“We know there are tremendous opportunities in the automotive and related advanced manufacturing sectors,” concludes Gillespie. “These industries are capital intensive and commercially focused with resources dedicated to R&D [research and development] advancement. We are confident that in the near future CNL will be regarded as a valued supply chain partner and an active participant in their respective product development and quality assurance programs.”
International discussions are also driving work in this area. The recently announced United States-Canada Clean Energy Dialogue, initiated by Prime Minister Stephen Harper and President Barack Obama, recognizes lighter-weight, sustainable materials as a key research area in the development of next-generation vehicles.
In addition to neutron beams, CNL is offering potential customers a wide range of expertise and facilities that it has been using to solve unique problems for clients outside the nuclear industry, including surface science tools and burst testing services, to name a couple examples.
About CNL
Canadian Nuclear Laboratories is a world leader in nuclear science and technology offering unique capabilities and solutions across a wide range of industries. Actively involved with industry-driven research and development in nuclear, automotive, aerospace, defence, security and life sciences, we provide solutions to keep these sectors competitive internationally.
With ongoing investments in new facilities and a focused mandate, Canadian Nuclear Laboratories is well positioned for the future. A new performance standard reinforced with a strong safety culture underscores every activity.
For more information on the complete range of services at Canadian Nuclear Laboratories, please visit www.cnl.ca or contact communications@cnl.ca.