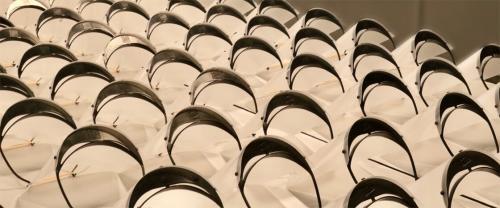
Innovation from Hatch allows projects to continue through pandemic
The COVID-19 pandemic has changed the way we work. This includes making sure projects and operations continue while protecting employees’ health.
Hatch Ltd. is using innovation to ensure their clients’ projects proceed while enabling employees to work virtually.
Not all consulting engineering companies have been able to adjust, meaning the nuclear industry is fortunate to have companies such as Hatch serving some of our critical players.
Hatch is offering its clients practical and cost-effective virtual approaches using innovative digital collaboration technologies to tap into expert skills and knowledge remotely.
This includes technology to remotely complete on-site inspections, which would have normally required a visit to the site. This allows maintenance staff to continue to perform asset maintenance and diagnostics, walk-throughs, inspections and training, while keeping everyone safe.
“The spread of COVID-19 has limited the ability of Hatch personnel to work on site to provide critical onsite services,” said Hatch technical specialist Blair Climenhaga in a video demonstration of the remote inspection and monitoring process. “To counter this, Hatch has expanded its services to offer remote assistance.”
The remote service supports video broadcasting from onsite using a phone, tablet, or hard-hat mounted camera to a remote expert receiving the video feed, he explained. The technology is optimized for the potential low bandwidth situations, which can be expected on site.
Team collaboration, even with physical distancing, is essential to continue executing projects and plant start-ups and performing day-to-day operations and maintenance.
The list of other ways this technology is currently used by Hatch includes:
- Collaborate with remote experts: Conduct meetings and workshops, directly from plant sites, enabling subject matter experts from around the world to share live content and interact in real time.
- Staff training and coaching: Senior Hatch staff are using these services and products to translate intangible knowledge into a centralized knowledge base of content. Trainers are being trained virtually, while new videos are being recorded for future training and record keeping purposes directly from the site.
- Guided plant tours: A media-rich, virtual guided tour for staff and partners with contextualized information and real-time conversations eliminating unnecessarily site visits.
- Inspection, troubleshooting and diagnostics: Hands-free and up-close inspection of assets in hazardous environments provides safer means of doing work. Maintenance crews now safely troubleshoot, assess, and rapidly resolve issues in the field.
Tell us your story
If you are a CNA member supporting the COVID-19 crisis response, please contact the CNA so we can spotlight your efforts.